Since the late 1980’s, Japan has largely depended on overseas production. Over the decades, this has resulted in over 50% of Japanese manufacturing existing overseas, largely in China, ASEAN countries, the US and Europe. This disposition relies on the benefits of a rules based regional environment through organizations such as the World Trade Organisation (WTO) for trade and investment. Amongst these external partners, the most recent and obvious has been Japan’s experience of integrating into regional production networks in China, transforming Japan’s role in regional dynamics. Gradually, as the demand and purchasing power of consumers in China increased, many of the Japanese companies already operating in China began to expand their supply chains to serve this new Chinese domestic market. Today, this historical expansion has made it increasingly difficult, and in some instances financially infeasible, for Japanese companies to move out of China.
Japan’s earlier experiences of supply chains disruptions
Japan faced similar challenges in 2011 to those it is currently facing with its excessive dependence on China. During this period, Japanese car and electronics firms’ supply chains were at risk due to large-scale flooding in central Thailand, occurring only months after the Tōhoku earthquake and tsunami that badly disrupted Japan’s own domestic production. During that time, Thailand based assembly plants were closed and production machinery was damaged or not accessible to component suppliers and workers. These plant closures and damages led to severe component shortages and a fall in company stock prices. The flooding also created problems for the country’s industrial manufacturers.
Japan’s investments in Thailand as a key production hub grew significantly since their start in the 1980’s, which is when the depreciation of the US dollar helped to send the value of Japan’s yen soaring. Thailand was also attractive as a production hub as it had good existing infrastructure, provided investment incentives, and allowed foreign firms to own the land that their factories were built on. Despite these advantages, Japanese car manufacturers (Toyota, Honda, Nissan, Mazda and Mitsubishi) responded to the flooding by seeking alternative production hubs overseas.
Although Japanese companies did not immediately shift out of Thailand, in the following years, rising wages and labor shortages prompted some Japanese manufacturing companies to adopt a “Thailand +1” strategy. These companies in turn looked for other new low-cost production sites in ASEAN, especially in the CLMV (Cambodia, Laos, Myanmar and Vietnam) economies. With burgeoning markets, Japan’s “Thailand +1” strategy encouraged investments in low-cost countries in CLMV, correspondingly expanding Japanese FDI as a leverage on regional production, human resources and cross-border infrastructure. These earlier established investments and relationships make ASEAN a natural fit for Japanese investments and production operations as the trend of relocation out of China grows.
The Tohoku earthquake in 2011 had also created unprecedented damage to Japanese domestic industrial supply chains. The supply of petrochemical complexes, which are mainly used for semiconductor manufacturing, had been drastically reduced. Supply chain disruptions also damaged local transportation system functionality, furthering the drop in Japanese exports in manufacturing goods to the US and other parts of the world. Aware of the geological and natural disaster related risks of having some of its core production plants within its own borders, Japan seeks to balance its domestic and overseas production as it continues to work with international partners to integrate into global supply chains.
Japan’s impetus to moving production out of China is actually not new
Over the last decade, Japanese companies have been moving out of China, though quite gradually. A 2019 survey suggested that there were 13,685 Japanese firms in China in May 2019, down from 13,934 in 2016 after reaching a peak of 14,394 in 2012. Economic factors have led some firms to expand their production capacity to supply an expanding Chinese market, while others have been moving their factories to Thailand, Vietnam and other Southeast Asian countries due to rising labor and foreign exchange costs in China. More recently, the US-China trade war has exacerbated this trend with a quarter of Japanese companies intending to reduce their China footprint due to geopolitical risks. JETRO survey results also suggest that the main reason Japanese company affiliates are considering reducing or shifting their operations in the next 1-2 years is due to decreasing sales in the local market and exports and increasing costs (e.g., procurement/labor costs) in China.
A 2019 survey by JETRO on ‘Business Conditions of Japanese companies in Asia’ suggested that over 35% of the companies felt they were negatively impacted in their China and Hong Kong/Macau operations due to changes in the trade environment. It seems quite evident that the main reason for negative perceptions was due to additional tariffs imposed by the US on Chinese products and then the retaliatory tariffs by China toward the US. However, out of the companies impacted, only 10% of them only planned or actually transferred production sites or changed procurement sources or sales destinations.
Covid-19 highlighted the growing risk of excessively depending on China. Growing distrust between Beijing and Tokyo’s global and regional supply chains have led Japan to rethink its Chinese operations. According to a February 2020 survey by Tokyo Shoko Research Ltd, 37% of more than 2,600 companies that responded were diversifying procurement to places other than China amid the Covid-19 crisis.
Japanese firms that depend exclusively on Chinese factories in their supply chains and firms that provide critically important goods for Japan’s domestic market will face the largest diversion. Due to the pandemic, the Japanese government expects a conservative and contracted approach in regional coordination, consolidating investments for domestic industrial security. This implies that Japan’s economic and trade interests shall be served at home first. For instance, Japan’s Ministry of Economy, Trade and Industry (METI) is planning to allure semiconductor companies like Intel and the Taiwan Semiconductor Manufacturing Company (TSMC) to move their core semiconductors and accessory facilities to Japan.
Government subsidies attempting to move Japanese companies away from China and back to Japan or elsewhere abroad provide protection and prevent exposure to trade disruptions. With Japan’s current subsidy program to help its firms shift out of China only applies to production of goods that either are important to public health and are strategically important or are manufactured largely in a few specific countries along with adoption of a ‘China Plus One’ supply chain management approach. Japanese reshoring and its potential subsidies to encourage this process may enhance domestic national security and benefit Japan’s small and medium-sized firms, boosting redevelopment plans and promoting domestic output of items that are largely imported. This may also help manufacturers of pandemic essential items, including face masks and sanitizers. Iris Ohyama, a Japanese firm that made masks in China has been taking advantage of these subsidies to diversify its operations from China.
How will Japan try to improve its supply chain security going forward
Japan is trying to improve its supply chain security amidst the pandemic while maintaining a positive economic engagement with China, as China is also a large market for Japanese firms. Even before the coronavirus pandemic Japanese companies had started shifting their production away from China due to the impacts of the U.S.-China trade war. Japan has also been keen in expanding its production with many ASEAN countries, in which it had already invested a net US$139 billion over the last decade (including Vietnam, Thailand, Indonesia, Malaysia and the Philippines). JETRO survey results suggest that Japanese firm affiliates have been more bullish on expanding their ASEAN operations than China since around 2011-12 (chart below) and the sentiments have remained consistent since then.
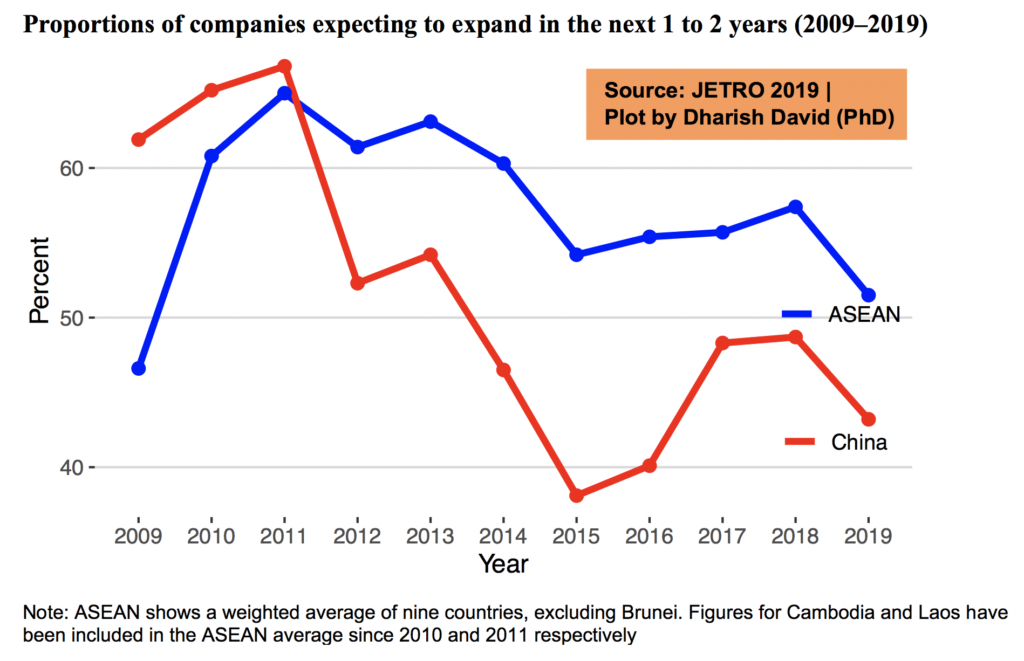
So for Southeast Asia, Japan is indeed the most trusted world power. Vietnam has emerged as a clear favourite for Japanese investment due to its relatively low labor and power costs, its openness to foreign investment, its business oriented government, and its young population. A large number of Japanese companies receiving subsidies are also moving to Indonesia, Thailand, Myanmar and the Philippines. In June 2020, Jakarta had made an announcement that three of the seven companies moving from China to Indonesia were Japanese. This added $850 million to Southeast Asia’s economy which included companies like Panasonic and Denso Corp. The post Covid-19 investments in ASEAN countries can prove profitable for Southeast Asia and also help Tokyo’s economic ambitions further grow.
Japanese companies are also planning to shift their production out of China to India or Bangladesh, reducing their regional dependences in East Asia and Southeast Asia. India and prominent Indo-Pacific members of the Regional Comprehensive Economic Partnership (RCEP) as well as Japan and Australia through the Resilient Supply Chain Initiative (RSCI) want to build resilient supply chains independent of China. The initiative was spearheaded through METI in cooperation with India, regarding the urgency of this recent initiative. Japan aims to attract FDI to the Indo-Pacific, transforming the region into an economic powerhouse as it builds relations with other like-minded partner countries, such as India and Australia, for a free, fair and predictable trade environment.
These moves by Japan and many other Western nations are already affecting China, as its economy still depends on being an integral part of global supply chains and maintaining manufacturing capital. The relocation of supply chains from China will continue to result in rippling effects across the high-value jobs market and purchasing power thresholds both in China and abroad. For Japan’s carmakers, reliance on Chinese suppliers in the world’s biggest auto market is still optimal. Companies like Toyota and Sony are keen to join the US and Europe in increasing their scrutiny of industries that are considered crucial to the national security of Japan.
Chinese media also claims that it will not be easy for Japanese companies to withdraw from China. Japanese companies understand the risks inherent in the Chinese government during the pandemic. China feels that Japan’s potential move might have a negative impact on wider foreign investor sentiment, demonstrating China’s ongoing need for access to rich western economies to regain stable growth post Covid-19.
Picture credits: MarineTraffic.com
Be First to Comment